Plastic extrusion for large-scale custom plastic parts
Plastic extrusion for large-scale custom plastic parts
Blog Article
Recognizing the Basics and Applications of Plastic Extrusion in Modern Production
In the world of modern-day manufacturing, the method of plastic extrusion plays an instrumental role. Unwinding the principles of this procedure exposes the true versatility and possibility of plastic extrusion.
The Fundamentals of Plastic Extrusion Process
While it might appear complicated, the basics of the plastic extrusion procedure are based on fairly straightforward principles. It is a production process where plastic is thawed and then shaped into a constant profile via a die. The raw plastic product, typically in the form of pellets, is fed right into an extruder. Inside the extruder, the plastic goes through warmth and pressure, creating it to melt. The molten plastic is then required with a designed opening, referred to as a die, to form a long, constant item. The extruded product is cooled down and afterwards cut to the wanted size. The plastic extrusion process is extensively made use of in numerous sectors due to its efficiency, cost-effectiveness, and adaptability.
Various Kinds of Plastic Extrusion Techniques
Building upon the basic understanding of the plastic extrusion procedure, it is essential to explore the different strategies involved in this production approach. In contrast, sheet extrusion produces large, flat sheets of plastic, which are usually more processed right into items such as food product packaging, shower curtains, and car parts. Understanding these strategies is crucial to using plastic extrusion effectively in modern-day manufacturing.

The Duty of Plastic Extrusion in the Automotive Industry
An overwhelming majority of parts in contemporary cars are products of the plastic extrusion procedure. Plastic extrusion is largely utilized in the production of various car components such as bumpers, grills, door panels, and dashboard trim. Thus, plastic extrusion plays a critical duty in auto manufacturing.
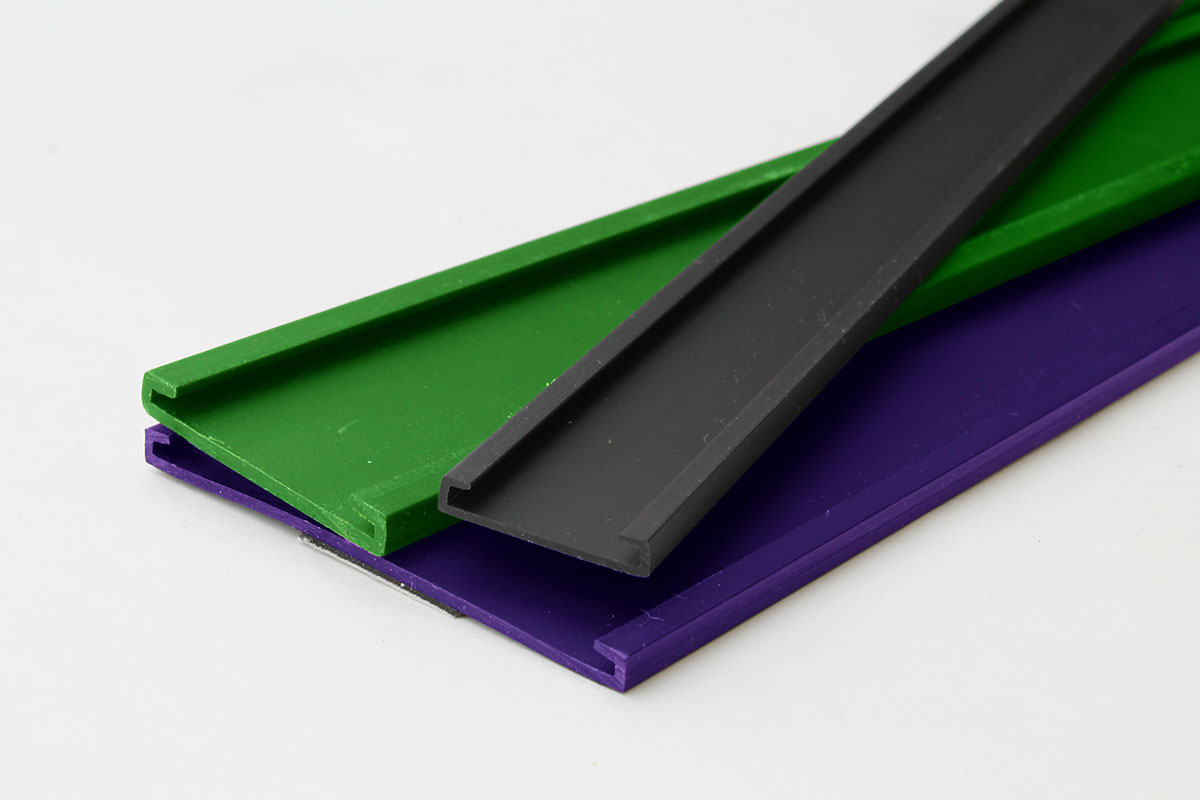
Applications of Plastic Extrusion in Consumer Item Manufacturing
Past its considerable influence on the automotive sector, plastic extrusion verifies just as reliable in the world of durable goods manufacturing. This procedure is critical in developing a large selection of items, from food packaging to household home appliances, toys, and also medical tools. The flexibility of plastic extrusion allows suppliers to make and create complex forms and sizes with high accuracy and performance. Due to the recyclability of numerous plastics, extruded components can be reprocessed, minimizing waste and price (plastic extrusion). The flexibility, versatility, and cost-effectiveness of plastic extrusion make it a recommended option for lots of customer goods producers, adding significantly to the industry's growth and development. The environmental implications of this extensive usage call for mindful consideration, a topic to be gone over better in the subsequent section.
Ecological Influence and Sustainability in Plastic Extrusion
The pervasive usage of plastic extrusion in making invites analysis of its environmental implications. Reliable machinery lowers power usage, while waste management systems reuse scrap plastic, decreasing raw product needs. Regardless of these enhancements, better development is required to reduce the ecological footprint of plastic extrusion.
Verdict
In final thought, plastic extrusion plays an important role in modern-day manufacturing, particularly in the automotive and durable goods fields. Its flexibility permits the production of a large view website range of elements with high accuracy. Furthermore, its possibility for these details recycling and advancement of biodegradable products offers an encouraging avenue in the direction of lasting methods, thereby resolving environmental worries. Comprehending the essentials of this process is essential to maximizing its advantages and applications.
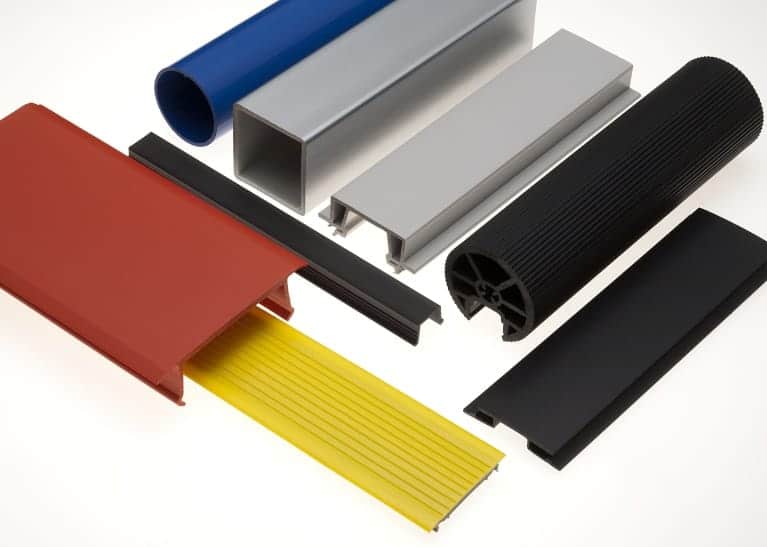
The plastic extrusion process is extensively utilized in different sectors go due to its effectiveness, cost-effectiveness, and versatility.
Structure upon the fundamental understanding of the plastic extrusion process, it is essential to discover the different techniques involved in this manufacturing technique. plastic extrusion. In contrast, sheet extrusion develops big, flat sheets of plastic, which are normally more refined into products such as food product packaging, shower curtains, and auto parts.A frustrating majority of components in modern-day lorries are items of the plastic extrusion process
Report this page